Ceramics in the broad definition of “inorganic solids” are one of the most important classes of materials next to metals, polymers, and composite materials. There are different types of ceramics, with technical ceramics (also known as engineering ceramics or high-performance ceramics) being the group with the highest mechanical, electrical, and/or thermal properties. Its high productivity is partly due to its extremely high purity, most of which are metal compounds combined with oxides, carbides, or nitrides. Ceramics can extend product life, increase efficiency, reduce overall maintenance costs, and increase productivity.
Technical Ceramic Material Group
Many groups of technical ceramics are available on the market today, but the basic classification defines them as highly effective components made of strong inorganic compounds. At the chemical level, they are usually held together by high-strength covalent bonds that form a strong structural lattice. The outstanding thermomechanical and chemical properties are maintained to the semi-crystalline microstructure and finally converted into solid monolithic ceramics.
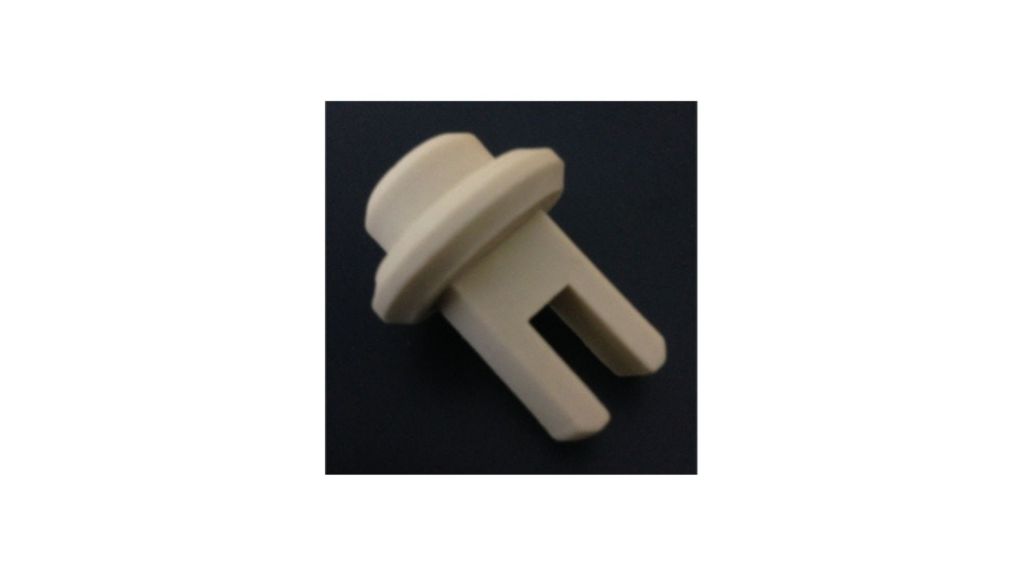
Multi-Lab supplies a wide range of high performance engineered ceramic materials including:
- Silicon Nitride (SiAlON): At Multi-Lab, we specialize in silicon nitride derivatives known as Sialons, outstanding universal engineering ceramics with fine-tuning
- Zirconium (ZrO2): With its incomparable durability, technical ceramics based on zirconium oxide are perfect for wear-resistant applications, from dentistry to metal forming.
- Aluminum (Al2O3): The technical ceramic of the same name, aluminum trioxide, belongs to the group of oxide ceramics and is the most used technical ceramic worldwide.
- Silicon carbide (SiC): With exceptional thermomechanical and non-corrosive features, technical ceramics based on silicon carbide are fitting for use in the chemical industry.
Read More – Applications of Technical Ceramics in Manufacturing Processes
Properties of Technical Ceramics
Chemically Inert and Corrosion Resistant
Technical ceramics are chemically very enduring and have moderate chemical solubility, which causes them extremely resistant to corrosion. Metals and polymers cannot allow the same inactivity or corrosion protection, making Macor or Machinable glass ceramics a very attractive option in several business and industrial applications, particularly when corrosion resistance is also needed.
High Hardness
One of the main general features of technical ceramics is their unusual hardness- some more than 3 times harder than stainless steel. This unusual hardness is instantly shown in its outstanding corrosion resistance, which indicates that several technical ceramics can manage their precision coatings with high endurance longer than other elements.
Excellent Wear Resistance
Many technical ceramics resist very high temperatures while preserving their construction and electrical qualities. When all elements and polymers start to decline, engineering ceramics will proceed to run with steady production and safety. These properties make ceramics suitable for use in very high-temperature applications such as ovens, jet engines, braking systems, and cutting tools.
Low density
Another common property of technical ceramics is their low density of 2 to 6 g/cm³. It is notably thinner than stainless steel (8 g/cc) and titanium (4.5 g/cc), with only the much more delicate aluminium having a comparable frequency. Due to their immense hardness and moderate density, technical ceramics are frequently being utilized in an extensive type of industries in applications where no other element can balance their production and strength.
Incredible Compressive Strength
Technical ceramics have very high strength, but these are only available under pressure. Many technical ceramics, for example, can withstand very high loads of 1000 to 4000 MPa. On the other hand, titanium, which is considered a very strong metal, only has a compressive strength of 1000 MPa.
Conductive or Thermal Insulation
Different types of technical ceramics have very different thermal properties. There are several ceramics (aluminum nitride) that have high thermal conductivity and are often used as radiators or exchangers in many electrical applications. Other ceramics are extremely less thermally conductive and are consequently suitable for a broad variety of applications.